STATE POLICE LOWER BASIN BARRACKS MODERNIZATION AND EXPANSION PROJECT
LOCATION:
BOSTON, MA
CLIENT TYPE:
MUNICIPAL
MARKET:
STORMWATER
WARREN PRODUCTS:
AT A GLANCE
• Critical tunnel rehabilitation
• Severe deterioration
• Structural enhancement
• Combined sewer overflow
• Carbon fiber reinforced pipe
• Longitudinal crack repair
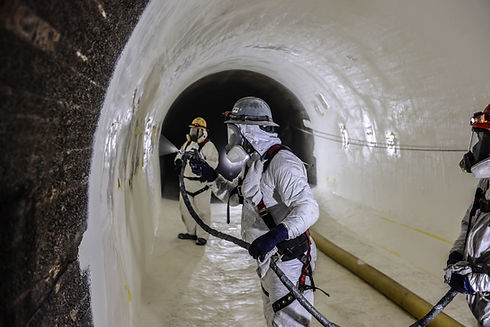
PROJECT BACKGROUND
The Massachusetts State Police Lower Basin Barracks Modernization and Expansion Project was a $22.5 million renovation and expansion project that began in the summer of 2021. Located at 250 Leverett Circle next to the Museum of Science and Storrow Drive, the project included the expansion and complete renovation of the historic Lower Basin Barracks for the Massachusetts State Police—a facility listed on the National Register of Historic Places. This scope of work included renovating the two-story barracks, parking lot, annex building, and recreational park and playground on the Charles River esplanade. Managed by the Department of Conservation and Recreation (DCR) of the Commonwealth of Massachusetts, Daniel O’Connell’s Sons (DOC) led the project as the general contractor with Finegold Alexander Architects (Finegold).
DOC needed clearance to operate heavy construction equipment and machinery on site. However, a critical 100-year-old 10-foot wide by 12-foot-high arched concrete combined sewer overflow (CSO) called the Boston Marginal Conduit (BMC) was located beneath the site. Owned by the Massachusetts Water Resources Authority (MWRA), the BMC is a dual-purpose structure that carries sewer while serving as a conduit for heavy rainwater to prevent flooding in downtown Boston. Once collected in the BMC, the overflow goes to the Deer Island Wastewater Treatment Plant—one of the largest wastewater treatment plants in the U.S. The aging system experienced infiltration, cracking, erosion, and microbial-induced corrosion from H2S gas exposure during its years of service.
It was unclear if the BMC could withstand HS-20 live loads, as the structure’s original design had only accounted for soil and hydro loads. As a result, MWRA began assessing the BMC’s existing condition and finding a viable trenchless solution to maintain its structural integrity while allowing DOC and other trades to work on-site began in the fall of 2021. MADERO Engineers and Constructors (MADERO) analyzed the feasibility of providing an engineering solution for the unreinforced concrete structure to handle live loads concurrent with the baseline design. As the Licensed Structural Engineer of Record, MADERO conducted a structural analysis through a three-dimensional (3D) structural engineering design. MADERO also performed an analysis calculation and provided engineering solutions for rehabilitating the BMC. This included an inspection, report, and an informational presentation for MWRA and other entities for approval.
The final engineering design was a robust composite structure with additional structural capacity for handling the required soil, hydro, and HS-20 live loads. MADERO also prepared the supporting engineered specifications for field installation and structural crack repair using Warren Environmental’s (Warren) epoxy coating system. Applying Warren’s epoxy would rehabilitate and structurally enhance the BMC to extend its surface life.
A&W Coatings had years of experience working for MWRA. The competing applicator’s proposed schedule to complete the project was longer than ours, highlighting the benefit of Warren’s high build, single coat system. Once the solution was approved, A&W was awarded the project as a subcontractor to DOC and mobilized to the site in March 2022.
SCOPE OF WORK
As DOC’s schedule largely depended on A&W’s scope, steel piles were first installed on either side of the structure with a bridge on top to avoid collapse. The bridge would allow heavy machinery to drive over the top without damaging the CSO below while we rehabilitated the tunnel. Warren’s structural epoxy was the best value method of trenchless technology for this unique application. The epoxy would reinforce the sections of the CSO in question, enabling DOC to continue their work even after removing the bridge. Our team approached the scope of work in three different sections to coat the structure’s entire circumferential area. This included two 25-foot sections and one 75-foot section. The BMC was approximately 650 feet long from the access point to the end of the tunnel.
A&W first performed surface preparation, including removing sediment and sludge buildup through power washing and abrasive blasting. MADERO inspected each surface for quality assurance before epoxy lining. Our crew mitigated infiltration with Warren’s 151-HG hydrophobic grout injection. We also repaired cracks with Warren’s 301-14 epoxy mastic and a spray-applied topcoat where required. In total, A&W repaired over 500 linear feet (LF) of cracks within the structure. With Warren’s 301-14 epoxy specified at 250 mils minimum, our crew spray-applied an average of 250-300 mils plus of epoxy in a single coat throughout the structure, fully lining its interior and enhancing its structural integrity. Following the application, MADERO inspected each lined section to verify that the field scope of work was performed per the requirements and acceptance criteria established in the engineering documents.
While power washing and abrasive blasting the substrate, our spray technicians discovered through-wall cracks in the BMC. The original design did not account for the unexpected cracks, requiring additional engineering calculations to determine the best repair method. MADERO’s updated engineering calculation results based on the assessment concluded that a carbon fiber reinforced polymer (CFRP) system would structurally reinforce the BMC. With the owner’s review and approval of the proposed repair plan, A&W forged ahead.
Our crew applied the CFRP and Warren's epoxy to repair the longitudinal cracks within the interior of the BMC and to the top exposed exterior side of the tunnel. We repaired longitudinal cracks on the interior crown of the last 40 feet of the pipe, located in the third and final section. As a result of our team’s success, we also lined three sewer manholes on site with Warren’s 301-14 epoxy as part of the general contractor’s scope.
PROJECT CHALLENGES
This was a successful project because of its complex nature and the project team’s ability to overcome logistical challenges. The job’s location presented several constraints. The site was set behind the historic Massachusetts State Police Barracks, near the course of the Boston Marathon and neighboring the Charles River. Daily rush hour traffic fed in from the nearby TD Garden Arena and Storrow Drive, a major parkway along the southern bank of the river. The site was also next to the Museum of Science, and minutes away from the Massachusetts Bay Transportation Authority’s (MBTA) Science Park/West End Light Rail Station and Amtrak’s North Station. The museum was a Boston Duck Tours departure location, causing an added layer of daily traffic. The site was also located next to an active public playground, requiring extra safety precautions.
The constrained site also presented logistical challenges in coordinating with the general contractor and various trades. The project required coordination with various entities involved, including DCR, MWRA, DOC, Finegold, specialty contractors, engineers, inspectors, union workers, and safety personnel. Working in the rainy, spring season presented schedule complications because rain events caused work delays. If rain was expected, our team requested approval from the MWRA to work. This would ensure the safety of our crew and prevent bypass equipment from getting lost down the pipe during high live flows. A&W removed all bypass equipment including hoses and pumps from the confined space for any expected or unforeseen rain events. Even low rainfall meant that our crews couldn’t work, which translated to lost time. It could take three to four hours to reinstall the bypass equipment, plus additional time to rewash any surfaces before lining.
ADDITIONAL PHOTOS
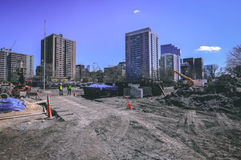
SAFETY CONSIDERATIONS
A&W prepared a site and confined space safety plan to ensure crew members and associated entities understood all potential hazards. We carried out all confined space safety measures for this project, but a third-party rescue service was on site for an added layer of protection. The third-party rescue members were on site for every manned entry into the BMC. Our crew worked through one entry point, a manhole that required an 18-foot drop down to the bottom of the BMC.
Monitoring the weather for rain was one of the biggest safety considerations and challenges. Any rainfall could become a safety hazard because the water runoff and sewer levels could quickly rise within the structure. A high level flow alarm was kept in the BMC at all times. This floating light and alarm system monitored the flow level and alerted our team if it would rise and become too high for safe manned entry.
PROJECT SUCCESSES
A&W managed key phases of the rehabilitation process on this high-profile project. This included collaborating with the engineer and architect on the initial condition assessment, performing surface preparation, and applying Warren’s epoxy while upholding quality and safety standards. Warren’s epoxy was the best value, trenchless technology solution proven to rehabilitate the BMC and benefit the MWRA. Most notably, Warren’s 301-14 epoxy structurally enhanced the BMC’s physical condition while the product’s versatility was compatible with the CFRP system to meet MADERO’s engineering calculations. The high build, single coat formula allowed for ease of application and adherence to DOC’s schedule. The zero volatile organic compound (VOC) formula was safe for the environment and the workers who applied it within the confined space. As a barrier coating to protect the concrete from future H2S exposure, A&W’s expert application of Warren’s epoxy was a long-term solution that exceeded the project’s needs.